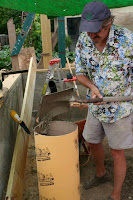
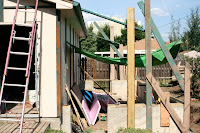
Digging was done. The cement was mixed and poured. We were done with the ditch witch, done insulating the footer. It was finally time to move above ground. Framing the greenhouse loomed ahead of us like a walk in the park, or perhaps a walk in the garden.
We wanted part of the south facing glazing to be at 60 degrees, which is perpendicular to the sun on December 21
st, and the other part to be at 30 degrees, which is perpendicular to the sun on June 21
st. These angles are ideal for growing plants.
A beam was needed to run the length of the greenhouse at that point. This proved to be tricky to set in exactly the right place, while tying it into the garage roof. The garage roof proved to be at 20 degrees. We decided to continue that angle down to the point where the 60 degree portion connected to it.
A post was also needed halfway to support the two 11 foot 2x10 beams. This post would end up being in the front raised bed, so we made the bottom portion a cement column that would not rot over time.
The beam was finally set at the exact right distance from the garage, so that the angle of the garage roof tied perfectly to it, as darkness fell onto our project. It was a
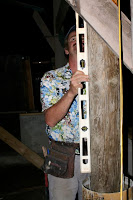
good feeling of a job well done.